THE POWER OF PREPARATION:
Electrical Preventive Maintenance: Save Time and Money
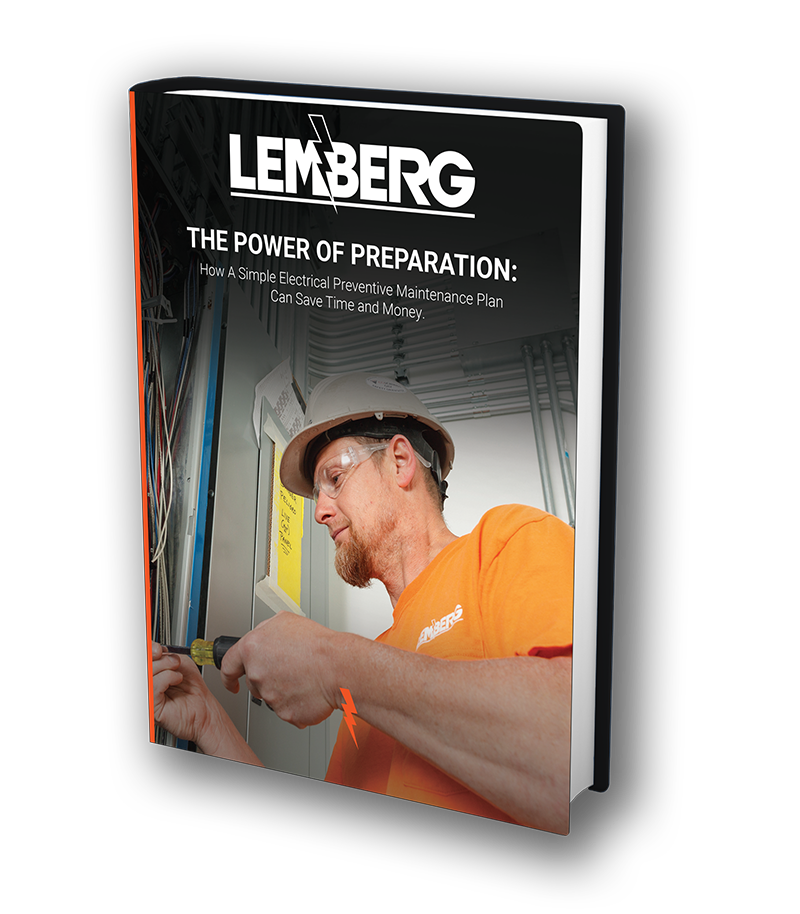
Download This Guide
Lemberg Electric is a leading provider of electrical services to various locations in Wisconsin, including Milwaukee, Dane, Rock, Racine, Kenosha, Walworth, Jefferson, Waukesha, Dodge, Washington, Ozaukee, Sheboygan, and Fond du Lac. With a team of highly skilled and experienced electricians, Lemberg Electric offers a comprehensive range of services, including electrical installation, repair, and maintenance.
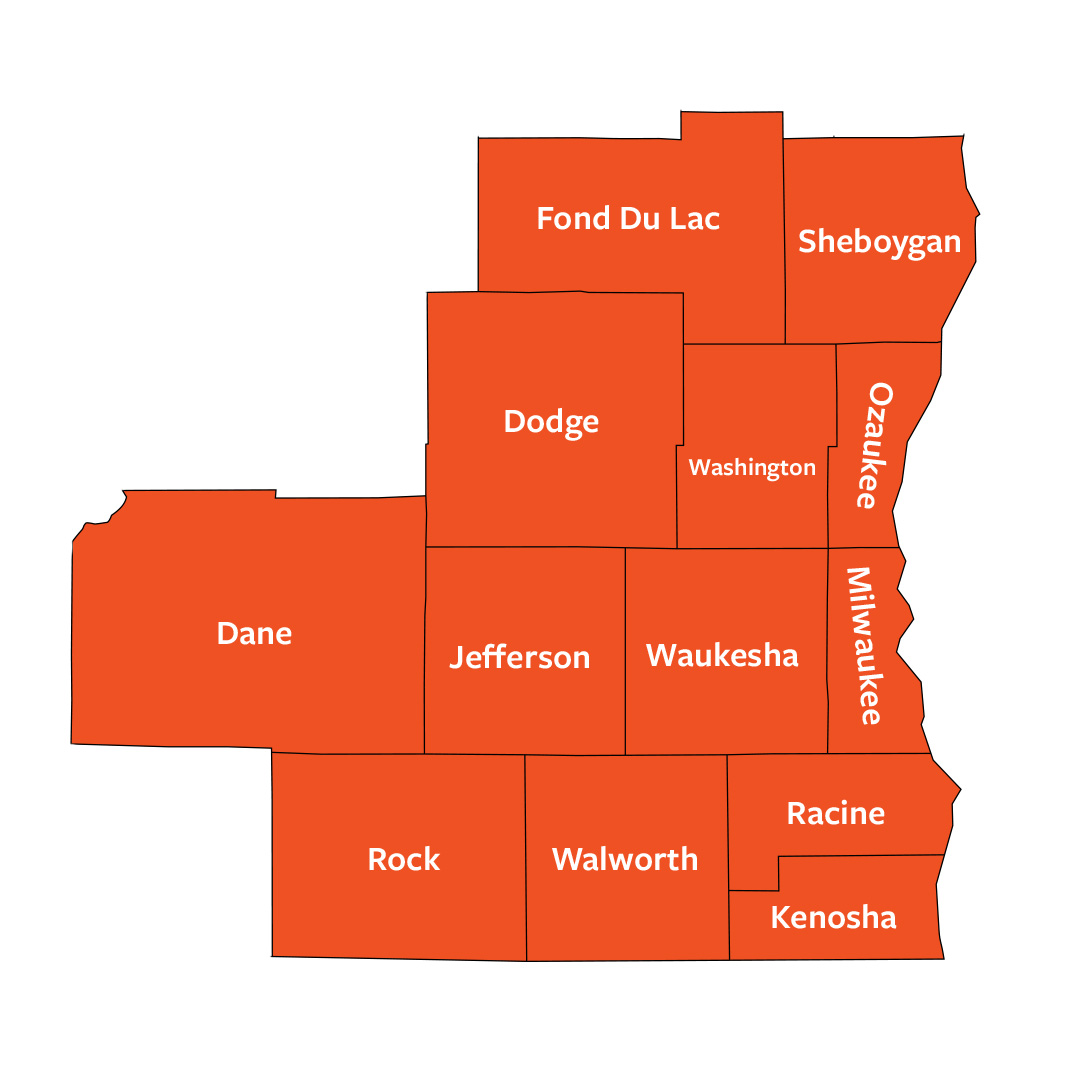
According to the NFPA, 24% of all fires in the industrial and manufacturing settings are caused by electrical distribution and lighting equipment. This is the leading cause of fires in these settings, followed by heating equipment. It is also the most preventable. Crucial to that prevention is electrical preventive maintenance. This is an easily preventable source of fires, which is why electrical preventive maintenance is so crucial to keeping these disasters from happening.
What’s more? The second leading cause of fires in industrial and manufacturing settings is heating equipment.
Twenty percent of all structure fires on industrial properties are caused by electrical failures or malfunctions, which is the leading cause of these kinds of fires. These fires happen mostly in processing and manufacturing areas where dust, lint, sawdust, excelsior and other fibers flammable liquids act as tinder.
Regular inspections are critical to detecting fire hazards like these. Proactive preventive measures will reduce the possibility for industrial fires.
Why Should Every Facility Have an Electrical Preventive Maintenance Program?
Without regular inspection and maintenance, equipment failure can lead to catastrophic safety hazards, inefficiency, and inflated maintenance costs. The average failure rate of electric equipment increases by 300% without an EPM program.There are many reasons a facility may not have an EPM program in place. One of the most common is budgetary restrictions. Often, budgets for proactive electrical maintenance programs are underestimated and underfunded. There is a belief among some facilities managers and financial decision-makers that the most fiscally responsible strategy is to wait until after a breakdown.
Often, decision-makers postpone or overlook proactive electrical maintenance for working machinery, seeing failure as the only indicator that maintenance is needed.
What they may not realize is that they can easily prevent equipment failure while spending less money and gaining more efficiency. The lack of mechanical maintenance can cause electrical failure. Poorly functioning machine components put additional stress on the entire machine. Electrical failure can happen when improper maintenance leaves machine components:
- Ungreased
- Misaligned
- Generally worn
There is a better strategy, though. You can prevent more than two-thirds of equipment failure by treating your electrical equipment the way you treat an automobile: by performing regularly scheduled checkups and maintenance.
Later in this guide, we’ll cover in-depth the benefits of electrical preventive maintenance.
How to Define Your EPM Routine
We know that electronic and electrical equipment degradation and failure is a matter of when not if.
Moving from a reactive approach to a proactive one, involves changes in thinking and practice. EPM routines are about inspecting, detecting, and correcting those problematic conditions before they cause outages, safety hazards, or other problems.
But the next question is: How?
At first glance, this concept may seem too imposing and too vast to accomplish. How do you monitor all the electrical equipment in your facility without anything slipping through the cracks?
Fortunately, many operations worldwide rely on EPM routines to prevent extremely catastrophic failures, and there have already been standardized routines developed. (Just think what would happen if degraded electrical equipment were used in environments such as the healthcare industry or the military.)
Routine Types of Electric Preventative Maintenance
The elements of any proactive maintenance routine fall into three categories (inspection, testing, and servicing) and include:
- Inventory: Every single piece of electrical equipment within your facility should be cataloged and ranked by the level of harm that would occur should it fail. These will become your inspection checklist. In this guide, you’ll find a pre-made sample checklist to get you started.
- Inspection: Every item on your inventory will have a regular inspection period. Some will undergo the standard inspection every year, but some -- such as critical equipment, or equipment used in conditions that cause faster wear -- will need to be inspected more often.
- Regular Observation & Testing: Observation is a great way to check for faltering components. Search for odd sounds, smells, or visual cues that indicate vibration. Look for dust and debris that can ignite. Though this is a great first line of defense against issues, it shouldn’t be the only way you monitor your equipment. There are times when extensive testing needs to be performed on the power distribution system to ensure reliability and to identify potential future failures.
- Record-Keeping: Extensive records should be kept of every piece of electrical equipment. This includes a report of every operational problem you encounter -- even the little ones, as well as all corrections, replacements, maintenance dates, contacts, etc. Every failure to boot up, every light that powers out for five minutes before powering back on, and every replaced screw should be logged. This will help your technicians troubleshoot what’s wrong with your equipment more quickly.
- Repair & Replacement: This is one of the final steps in your routine. Any faulty or underperforming equipment must be adjusted, repaired, or replaced based on its needs. It’s also a good idea to build a parts list for each machine as well as documentation from the manufacturer that may help with correct part identification, ordering, and troubleshooting.
- Analytics: As with any extensively detailed dataset, there’s great value in keeping meticulous records about your electrical equipment. Over time, you’ll build up enough data to confidently predict the behavior and durability of your equipment. You can use this information to refine your EPM procedures and make them, even more, cost-effective.
On Friday, November 21, 1980, inside a Las Vegas hotel restaurant called The Deli, an improperly installed refrigerated display case caught fire.
Had the machine been inspected regularly, someone would have noticed either the ungrounded conduit, or the improperly installed fan, and disaster might have been averted. Instead, The Deli -- and the entire first floor of the MGM Grand Casino and Resort where it was located -- was engulfed in flames.
Eighty-five people were killed and 627 more were injured. MGM Grand Hotels lost $1 billion. Because the MGM Grand was one of the largest tax contributors to the local gambling industry, the closure cost the local government about $1.7 million.
It remains to this day the deadliest disaster in the history of Nevada, and the third-deadliest hotel fire in modern U.S. history – and one that may have been avoided with an electrical preventive maintenance plan.
Measuring the Benefits of Electrical Preventive Maintenance
As we’ve seen, an organized EPM program is about more than just equipment functionality. It’s about protecting both your investment, and your community: that means your employees, customers, and neighbors.
Financial Benefits
The most basic financial benefits of EPM are right up front: electrical failures, electrical fires, and equipment outages cost big dollars. In fact, electrical failure costs businesses millions of dollars in losses annually. Having a proactive EPM plan is shown to reduce most major problems, minimizing the need for expensive reactive maintenance.
But the cost of an equipment failure isn’t just immediate. There are also secondary financial repercussions, such as payouts when injuries happen in unsafe workspaces, higher electricity costs from inappropriately calibrated machinery, not to mention expensive equipment replacements.
Operational Benefits
Electrical preventive maintenance helps facilities achieve maximum operational efficiency and reliability. As a result of EPM maintenance practices, there are fewer unplanned downtimes. When they do occur, they’re shorter and more predictable.
When EPM isn’t employed, operational efficiency suffers drastically. Often, the malfunctioning equipment refuses to reveal itself without a detailed inspection that requires a mechanical or facility shut down.
Compromised systems or components such as circuit breakers or relay switches will cascade problems downstream and compromise additional systems. -- headaches that can be avoided with regular proactive EPM routines.
Safety Benefits
Electrical machinery is dangerous, and there are strict safety codes and precautions employees must take to use it. When something out of the ordinary happens with the machinery, the stakes are raised.
In the case of the MGM Grand Hotel and Casino, thorough electrical preventive maintenance could have saved dozens of lives, by alerting maintenance staff to dangerous electrical hazards early, before they caused deadly problems.
EPM also helps protect critical safety equipment such as fire alarm systems, generators, UPS systems, emergency, and egress lighting. Many of the front line defenses used for safety in commercial facilities can be kept in functioning order with the right proactive maintenance protocols.
The Cost of Repair vs. Replacement
Taking a reactive approach means the ultimate moment of equipment failure will be an unknown, unpredictable challenge you’ll have to face – likely sooner than necessary.
Unplanned shutdowns due to equipment failures are just that – unplanned. They are never convenient.
More often than not, your equipment will fail in the middle of operations causing production delays. You could try to schedule emergency repairs on short notice, but you’ll still have to pay premium service costs for the effort.
When machinery breaks down due to neglected inspection and maintenance, it’s often too late for simple repairs. This is where those hefty costs come in.
Worse, when it comes to electrical distribution systems, new equipment doesn’t always replace the failed equipment in a 1:1 way. Modifications may be needed to make the system work, further adding to your costs. There are many times when replacement electrical parts are non-stock or obsolete items which cause even a bigger delay in getting your equipment back online.
Inventory Creation and Checklist Development:
Building an inventory and proactive maintenance checklist that’s customized to your facility is one of the most critical steps in developing a new EPM program. It's recommended you consult a qualified professional during this process. Without prior knowledge, it's easy to overlook less obvious pieces of equipment.
For instance, it’s important to include the building’s internal electrical distribution system on your checklist. Additionally, many facility managers are under the false impression that electrical equipment without moving parts won’t break down. The truth is, this equipment needs to be monitored and maintained just as frequently as the rest.
When building your customized inventory and checklist, you should:
- Identify and denote critical, high-value systems.
- Consult manufacturer documents for recommended maintenance windows.
- Use the data in your records to fine-tune the schedule for equipment that may need proactive maintenance a little more often than previously anticipated.
Scheduling
When first establishing your EPM schedule, it’s important to understand that this process will be tricky and may require some fine-tuning as you go along. It’s also important to understand the difference between the three primary types of scheduling, which are:
- Calendar-Based: Inspections, detections, and corrections performed on a regularly scheduled basis based on the date or interval of time between previous maintenance.
- Predictive: Inspections and maintenance performed because something has caused suspicion of a looming breakdown.
- Prescriptive: Inspections and maintenance performed as a result of a breakdown.
The goal of EPM is to rely on calendar-based scheduling as much as possible while implementing predictive maintenance only when necessary.
How often should you schedule a system-wide EPM inspection? The answer is multi-faceted.
First, most electrical manufacturers recommend a period of two to three years. This should be the absolute longest interval between maintenance and inspections on your equipment.
However, some of your equipment should be checked in between those system-wide inspections. These include:
- Critical pieces of equipment (such as equipment that would cause dramatic service outages or safety hazards in the event of a failure).
- Equipment used in harsh or external environments that may be exposed to sand, dust, moisture, corrosive road salt, or other materials causing faster degradation.
- Equipment with more frequent maintenance recommended by the manufacturer.
- Verifying electrical equipment enclosures are rated for the environment they are installed to protect the interior components. This happens all too often and almost always leads to premature failures.
Consulting with an experienced engineer while building your schedule can help you make sure that you’re attending to all of your machinery frequently enough.
Record-Keeping
Record-keeping is one of the most overlooked components of an EPM routine. However, it’s fundamental to the ultimate goal of trimming down costs without sacrificing safety or productivity.
It also allows for accurate metrics to measure your facility’s full-electric KPIs (Key Performance Indicators).
A competent electrical preventive maintenance record includes:
- An itemized list of all electrical equipment in the facility.
- A list of wear and damage on all electrical equipment, including critical damage that impedes operation or may soon impede operation, as well as non-critical damage.
- EPM procedures and repairs are performed on each piece of equipment in the facility, including those that happen outside of regularly scheduled maintenance.
- An inventory of all spare parts stored within the facility.
- A list of outages and abnormalities involved in every piece of equipment in the facility.
- Important documents such as instructions, schematics, warranties, and any other official paperwork.
- Performance records including things like production results, which would show the correlation between performance and maintenance, such as machine performance based on smooth-running and reliable parts or machines, as well as improved employee performance as a result of well-lit, smooth-running, and safe working environments.
Keeping careful records ensures timely inspections and repairs. It tracks the results of tests over time to help identify potential failures. It also informs your technicians of machinery that may be overdue for maintenance and helps them troubleshoot problems.
A clear, concise, preferably digital record-keeping system will reduce the average amount of time from failure to repair.
How to Hire Qualified Electrical Personnel
Inspecting, testing, and repairing electrical equipment is best performed by qualified, licensed electricians. The people who perform your EPM procedures should be trained in the use and maintenance of every piece of equipment on your property. Certain vital pieces of equipment, such as electrical distribution systems, require additional certifications.
When considering assistance with your electrical systems and maintenance, be sure you are aware of their qualifications and experience. It's important to know the difference between an entry-level electrician and a journeyman, so you’ll have a better idea of what to expect from their work, or what to look out for.
The varying levels of experience include:
Apprentice: Because the duties of an electrician are varied and critical, electricians spend 3 to 6 years training on the job and in the classroom as an apprentice. An apprentice is someone currently engaged in that training. They may have the experience, but they are not certified to work without the supervision of a higher-ranking electrician.
Journeyman: Journeyman electricians have passed skills and knowledge test in order to receive their license. They are qualified to work independently on most electrical components. Once they have the qualifications necessary, they may elect to test for the Master Electricians license in their state.
The requirements a journeyman must meet to be licensed vary by state. However, they typically include:
- Five years and 8,000 hours of on the job experience.
- 1,100 classroom instruction hours.
- Completion of certification testing that verifies jobsite experience, knowledge of electrical codes, and the ability to understand schematics and technical material.
Master: Master electricians have expanded experience and expertise and have passed skills and knowledge tests to receive licensing. In Wisconsin, Master electricians have fulfilled the following requirements:
- Completed 12 months of experience as a licensed journeyman electrician.
- Logged experience in installing, repairing, and maintaining electrical wiring over the course of at least 60 months, accruing at least 10,000 hours of experience during this time OR at least 1,000 hours per year for at least 7 years.
Hazards That May Appear During Inspection:
The controlling theme of your physical EPM inspections should be to keep your equipment clean, dry, and tight. This will keep stray debris and moisture from entering and causing damage. It will also keep loose parts from causing more damage.
The most frequent cause of electrical distribution failures are loose connections or parts (which cause around 30% of electrical distribution outages) and exposure to moisture (which causes around 17% of outages). Together, these cause approximately 50% of all facility power outages.
Loose connections and parts are hazardous (like we saw earlier in the case with the MGM Grand Hotel and Casino) because they can lead to erratic operation, unintended load distribution, and power fluctuations. Moisture can interfere with electrical conduits and cause short circuits.
A number of other common problems include:
- Line disturbances
- Foreign objects
- Defective, improperly installed, or inadequate installation
- Exposed wiring
- Load changes or additions
- Circuit alterations
- Potential for collision
- Improperly set or selected protective devices
- Lightning damage
- Overloading or inadequate capacity
- Dust, dirt, and oil
- Temperature extremes (both hot and cold)
Remember, not all damage to electrical equipment is caused by human error. General “wear and tear” is standard with all machinery. As such, it’s important to track all degradation over time. The effects of which are especially multiplied in environments with harsh weather or dramatic cold seasons.
Pre-Outage Infrared (IR) Scan
Occasionally, you will need to have planned downtime to inspect all instruments and make necessary adjustments. It’s a good time to get an overview of the total health of your system and it’s the perfect time for intensive testing.
Before your scheduled outage, it's prudent to conduct a thermographic inspection, also known as an Infrared (IR) Scan, of cable and bus connections, switchgear, motor control centers, distribution panels, and starters. This inspection should be done during a peak load time to accurately gauge equipment stress.
These tests are critical in preventing equipment failure. They help detect connections that need to be cleaned or tightened, circuits that are overloaded or imbalanced, or improperly installed equipment.
During this proactive electrical maintenance test, a technician uses an infrared camera to read for high-temperature excursions -- a likely sign of loose connections, failed components and load imbalance. Aside from the occasional closing and re-opening of circuit breakers and switches during the testing phase, thermographic testing is non-invasive.
During the inspection, an early list will be made of equipment that will likely need to be tuned or repaired -- ultimately helping facility teams focus their resources in the right areas when the power is shut down for a scheduled outage.
A thermographic inspection should only be done by certified thermographers using specialized equipment. They have the necessary education, experience, and judgment to determine the best course of action (for example, whether a device should be repaired or replaced) based on test results.
Other Testing and EPM Procedures
After the scheduled outage is in effect, there are other tests that will reveal the health of your equipment that can be performed by a contracted specialist. These include:
- Relay and Circuit Breaker Tests: Relays and circuit breakers are protective trip devices that need to be routinely checked for functionality.
- Oil Tests: Transformers, circuit breakers, and disconnect switches all use oil to function. This oil needs to be sampled and screen-tested to determine its quality.
- Dissolved Gas Test: Oil from transformers can be dissolved into gas, and the gas tested, which can reveal any problems within the unit.
- SF6 Gas Leak Testing: Equipment that runs on SF6 gas will need to be tested to ensure the integrity of the gas system.
Additional EPM checklist items:
- Check and test all transformers
- Inspect and test arc fault circuit breakers (AFCI)
- Inspect and test ground fault circuit breakers (GFCI)
- Inspect and test voltage regulators
- Check electrical panels
- Verify metering works correctly
- Check and clean motor controls
- Inspect and test switches and gears
- Inspect the distribution and termination of the wiring
- Check all grounding and overcurrent protection devices
- Inspect lights and light fixtures, including:
- recessed
- tracking
- security
- motion-sensored
- parking lot and garage
- HID
- fluorescent
- Ballast and lamp replacement
- Special systems, such as:
- generators
- alarm
- Uninterruptible power supply (UPS) systems
- surge protection for a building
- telecommunications
- video and cable
- battery power
If it’s time for your company to expand or establish your electrical maintenance program, we’re your Milwaukee-area full-service partner. Our complete list of electrical services includes:
- Technical Support
- Preventive Maintenance
- 24-hour Emergency Service
- Infrared Testing Technology
- Industrial Electrical Repair
- Design Assistance
- Variable Frequency Drives
- Machine and Process Control Wiring
- Renewable Energy Sources
- Photovoltaic Solar Panel Integration
- LED Replacements and Retrofits
- Energy-Efficient Fixtures
- Building Automation Systems/HVAC Controls
- Occupancy Sensor for Touch-Free Lighting
- Air Filtration and Sanitizing Systems for Virus-Free Environments
- Electric car charging systems
- Electricians licensed through the Milwaukee Electrical Joint Apprenticeship Training Program (MEJATC)
Lemberg is the one-stop shop for electrical maintenance, repair, and troubleshooting, proudly serving businesses in Milwaukee and Southeastern Wisconsin. We’re customer-service-driven, provide prompt service from licensed technicians 24/7, and it’s our mission to be your preferred provider with a personal touch.
Lemberg Electric, Inc., (262)781-1500, Info@LembergElectric.com